The smart rack label
The smart rack label
iDisplay: the multifunctional digital rack label
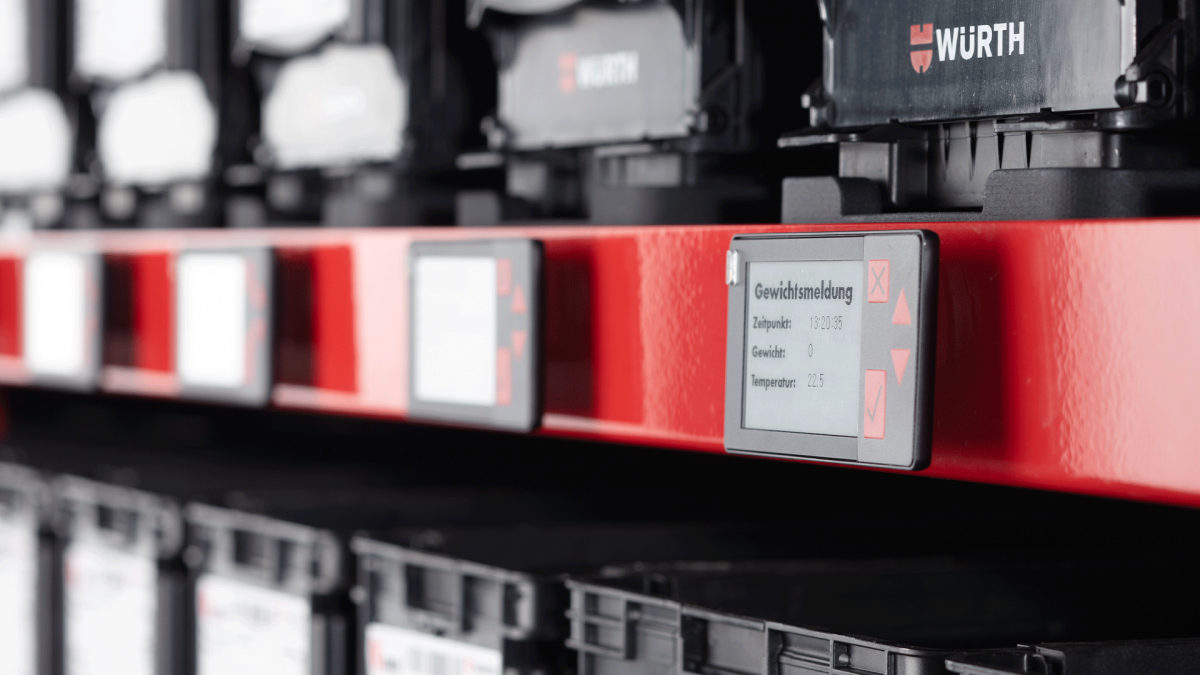
Rack label with added value
More efficiency and transparency in your production
With its iDISPLAY, Würth Industrie Service presents an innovative solution that replaces the traditional rack labels with digital displays. In this way, all the important inventory and order data is available directly at the rack – quickly, precisely and always up to date. Item numbers, fill levels, availability and storage locations are shown on the display in real time, and the data is automatically updated and synchronised thanks to the seamless connection to your ERP system.
This makes manual input a thing of the past and the iDISPLAY a real booster for your production supply.
iDISPLAY: One label – Four functions
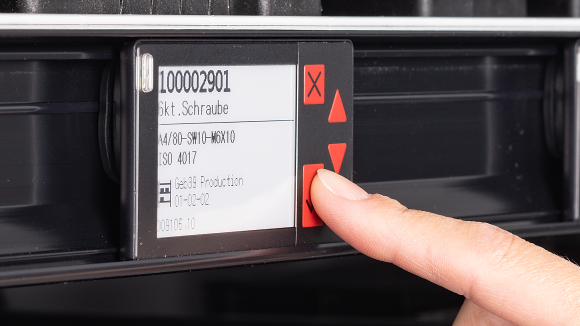
iDISPLAYrack – Item information at a glance
Every iDISPLAY is directly connected to the ERP system of Würth Industrie Service, and delivers real-time data, which can be retrieved quickly, easily and directly at the storage location: starting from the item number, item text, filling quantity to storage area and storage location up to the bin type, inventory, availability of bins, filling status as well as upcoming filling dates. Since the system is updated automatically in case of any major changes in master data, the customers are always up to date.
Thus, iDISPLAY replaces the paper label on the Kanban rack, and those who are picking the order can easily retrieve the information they are looking for by navigating using two display pages.
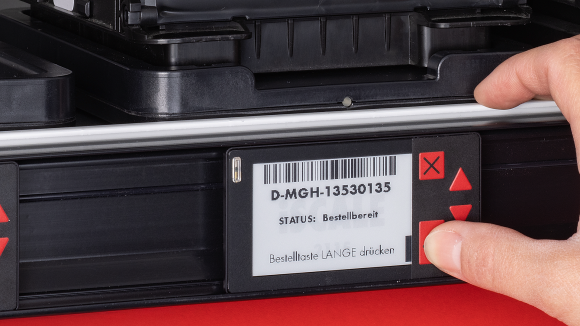
iDISPLAYpush – Reordering at the push of a button
The iDISPLAY enables orders to be triggered directly at bin level within seconds at the push of a button. Once an empty signal is triggered, the current status is displayed until the filling is complete, which means that a new order can only be placed afterwards.
By making all the data digitally available at any point of time, manual errors can be minimised, which allows the customers to rely on maximum productivity and transparency.
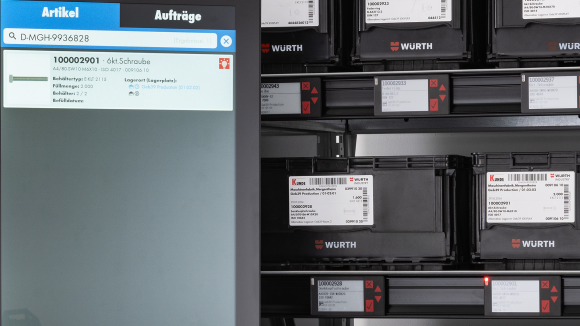
iDISPLAY & iTERMINAL – Search-by-Light
iDISPLAY can reach its maximum potential when combined with the digital information board iTERMINAL.Together, these two systems can help you to find the required item within seconds:
1. Start search – Enter the item number in the search field or scan the barcode
2. Visualise – The LED on the corresponding iDISPLAY of the rack location lights up immediately.
3. Withdraw the item – This eliminates long search routes, thus saving significant time.
Thus, the two systems combined reduce the search time significantly and ensure higher productivity in the production workflows.
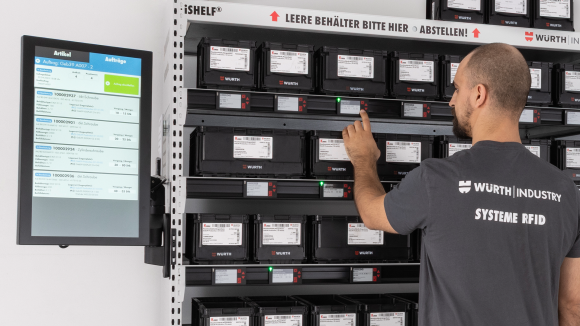
iDISPLAY & iTERMINAL – Pick-by-Light
Through the connected systems, it is not only possible to just initiate the search for items via iTERMINAL, but also to get assistance in picking using the “Pick by Light” function.
With the help of the LED signal, the iDISPLAY shows the exact location of the item required for the next step of the process, while the quantity to be withdrawn is also automatically displayed on the display. Up to six picks per item can currently be shown simultaneously and those who are picking can navigate through these on the display.
By connecting the customer's ERP system to the iTERMINAL, pick lists can be transferred from the customer and accessed on the iTERMINAL, making it possible to pick the items using the iDISPLAYs. Manual intervention is no longer necessary.
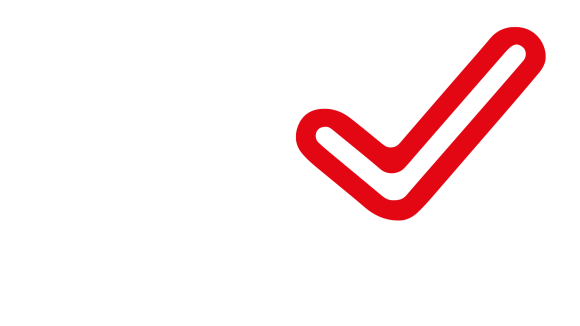
- All item information available digitally:
Item number, item text, filling quantity, storage location, storage area, bin type, stock, bin availability, filling status and upcoming filling dates. - Real-time updating of the item information
- Re-ordering at the push of a button
- Simplified item search using the Search-by-Light function
- Simplified picking using the Pick-by-Light function
- Error minimisation through the elimination of manual processes
- Increased productivity thanks to reduced search and picking times
- Resource-saving system (printed item or pick lists no longer required)
- Application is available in different languages
More Kanban solutions
You might find this interesting:
Contact:
We are here for you!
Contact us at + 49 7931 91-0 , by sending an e-mail to cteilemanagement@wuerth-industrie.com or by filling our
The Würth Industrie Service GmbH & Co. KG collects and processes the personal data provided in the form in order to process the requested request for you. Please note the mandatory fields in the forms. The legal basis for this processing, the absolutely necessary data, is Art. 6 para. 1 lit. b DSGVO, implementation of a pre-contractual measure. The processing of data voluntarily provided by you is carried out on the basis of Art. 6 para. 1 lit. f DSGVO. Thereafter, processing is permissible which is necessary to safeguard our legitimate interests. Our legitimate interest is to have contact with you, our customers, to improve our consulting quality and to be able to contact you more easily in case of possible queries. The data collected will only be stored by us for as long as is necessary to process your enquiry and to contact you. They are then deleted.
Supplementary data protection information, in particular regarding your rights to information, correction, deletion, restriction of processing, objection and complaint, can be found in our data protection declaration.